KDV’s DN150 SS Body Weir Type Diaphragm Valve
KDV has successfully wrapped up a project for a chemical processing plant in the UK, highlighting our ability to deliver custom valve solutions with quick lead times. Now ready for dispatch are our DN150 Stainless Steel Weir-Type Diaphragm Valves—designed to deliver the strength, precision, and reliability needed for demanding chemical processing applications. These valves are more than just robust components; they embody the perfect combination of durability and performance for complex industrial environments.
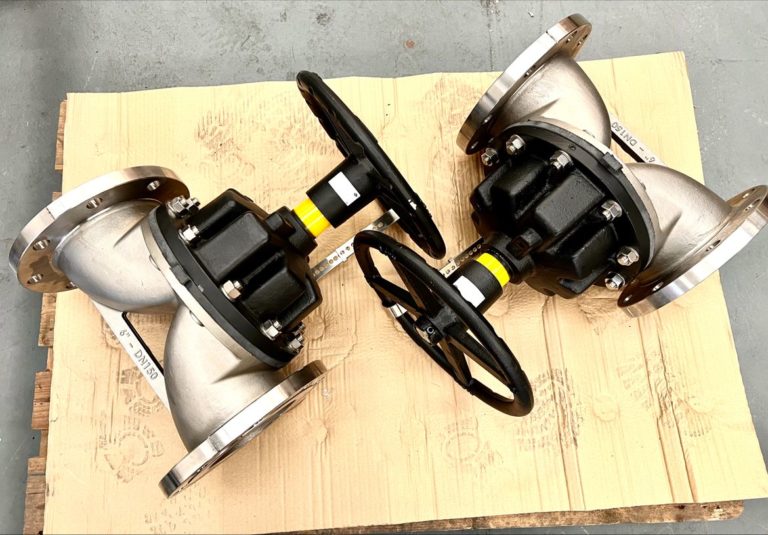
Features and Benefits of a Stainless Steel Diaphragm Valve Weir Type
This stainless steel valve is key in the diaphragm valve market, offering smooth flow control and easy upkeep. It’s perfect for sanitary and sterile uses, ensuring cleanliness in industries like food and pharma. Durable and chemical-resistant, it’s also great for industrial applications. Outstanding qualities include:
Bubble-Tight Shutoff for Complete Leak Prevention
One of the standout features of these valves is their bubble-tight shutoff, providing a completely leak-proof seal. This is critical for maintaining process integrity, preventing contamination, and ensuring that your operations remain safe and efficient. It not only enhances safety but also reduces downtime, keeping everything running smoothly.
Low Maintenance, High Uptime
A major advantage of the DN150 valves is their low maintenance design. By reducing the need for constant repairs or replacements, these valves ensure that operations can continue without frequent interruptions. This means reduced maintenance costs and more focus on productivity, helping to maximise uptime and minimise unnecessary disruptions.
Easily Accessible Spare Parts for Uninterrupted Operation
At KDV, we ensure that spare parts, including those necessary for diaphragm valve replacement, are always readily available. This means any repairs or maintenance can be completed swiftly, keeping your system operational. The availability of diaphragm valve parts helps ensure that your valves remain in top condition, further reducing potential downtime and keeping your processes efficient.
In-Line Serviceability for Easy Maintenance
The top-entry design allows for in-line serviceability, meaning the valve can be maintained without being removed from the pipeline. This feature saves significant time and labour, ensuring that your system can be serviced with minimal disruption. This is especially important in industries where extended downtime is not an option.
Cavity-Free Design for Cleaner Processes
The cavity-free design eliminates the risk of media entrapment, reducing the potential for contamination or blockages. This ensures a cleaner operation, particularly in applications where maintaining the purity of the process is crucial, such as in chemical processing or pharmaceutical manufacturing.
Low Fugitive Emissions for Environmental and Safety Compliance
These valves are designed to keep fugitive emissions to a minimum, helping you meet strict environmental and safety regulations. By reducing emissions, you’re not only creating a safer working environment but also ensuring compliance with environmental standards and supporting sustainability efforts.
No Stem Seal Leakage for Improved Durability
The no stem seal leakage design boosts durability, especially in harsh environments like chemical processing. The absence of stem seal leaks enhances reliability and safety, ensuring the long-term performance of your system, even under the most demanding conditions.
Line Media Isolation for Extended Valve Life
Line media isolation protects the valve internals from exposure to the processed media, significantly extending the life of the valve. This feature ensures that the valve remains operational and reliable over time, even in applications where it faces corrosive or abrasive materials.
What Makes Diaphragm Valves Unique?
You might ask, what makes a diaphragm valve different than all other valves? The answer lies in its design and function. Diaphragm valves use a flexible diaphragm to regulate the flow of media, offering a combination of tight sealing, easy maintenance, and excellent resistance to contamination. These valves excel in applications where hygiene, safety, and precise flow control are paramount—making them indispensable in industries such as chemical processing, food and beverage, and pharmaceuticals.
Rigorous Testing and Quality Assurance
BSPP Standards for Uncompromising Quality
Each KDV DN150 valve undergoes stringent testing to meet British Standard Pipe Parallel (BSPP) standards. These tests ensure that every valve, across all diaphragm valve types, delivers consistent, reliable performance in even the harshest industrial environments. Meeting these standards guarantees that our valves are built to last, providing peace of mind and consistent results.
Proven Reliability in Critical Applications
Passing these rigorous tests is a testament to the quality and reliability of KDV valves. For our customers, this translates to trust and assurance—knowing that their operations are backed by valves that have been engineered to perform in demanding conditions. Whether you’re handling high-pressure applications or corrosive materials, these valves are designed to keep your processes running smoothly and safely.
Final Inspection for Ultimate Quality Control
Before dispatch, each valve undergoes a thorough final inspection to ensure it meets the highest quality and performance standards. This step guarantees that the KDV DN150 valve is ready to handle the rigours of industrial use, particularly in the challenging environments of chemical processing plants. Our meticulous quality control process ensures that every valve is fit for purpose from the moment it arrives.
FAQ for Stainless Steel Diaphragm Valve Weir Type
- What is a weir diaphragm valve?
A weir diaphragm valve is a type of valve with a raised, saddle-shaped internal body that helps regulate flow. It uses a flexible diaphragm to seal off flow and is highly effective for precise flow control and preventing leakage. - What makes stainless steel diaphragm valves ideal for industrial applications?
Stainless steel diaphragm valves (SS diaphragm valves) are durable, corrosion-resistant, and suitable for handling aggressive chemicals. Their robust design ensures reliability in demanding industrial settings. - What are the advantages of a sanitary diaphragm valve?
Sanitary diaphragm valves are designed for industries like food, beverage, and pharmaceuticals, offering smooth surfaces and cavity-free designs to prevent contamination and ensure easy cleaning. - How does a sterile diaphragm valve support critical applications?
Sterile diaphragm valves maintain process purity, ensuring no contamination in sensitive applications such as pharmaceutical manufacturing and high-purity chemical processes. - What is the role of lined diaphragm valves?
Lined diaphragm valves are used in applications where additional protection against corrosive or abrasive media is required. The lining shields the valve body from damage, extending its life. - How does in-line serviceability improve maintenance?
The top-entry design of these valves allows for easy in-line maintenance without removing the valve from the pipeline, reducing downtime and labor costs. - What is the importance of low fugitive emissions?
Low fugitive emissions help meet environmental standards, create a safer workplace, and support sustainability efforts by minimizing leaks of harmful substances. - Why is bubble-tight shutoff essential?
Bubble-tight shutoff prevents leaks, maintaining process integrity and enhancing safety while reducing downtime and maintenance costs. - How does line media isolation extend valve life?
Line media isolation prevents processed media from contacting valve internals, protecting components from corrosion and wear, ensuring longevity. - What sets KDV diaphragm valves apart?
KDV valves undergo rigorous testing to meet BSPP standards, ensuring reliable performance, high durability, and suitability for harsh industrial environments.
By integrating features such as cavity-free design, robust materials, and rigorous quality assurance, KDV valves deliver unmatched performance across the stainless steel diaphragm valve market. Explore their capabilities for industrial, sanitary, and sterile applications to enhance your processes.
Enhance Your Operations with KDV’s High-Performance Valves
If you’re looking to integrate high-performance valves like the DN150 Stainless Steel Weir-Type Diaphragm Valve into your system, or need more details on specifications, get in touch with us today. Our team is ready to assist with custom solutions that will enhance the reliability and efficiency of your operations. With KDV valves, you’re not only investing in quality equipment but also in the long-term success of your industrial processes.